Introduction to Fabrication Solutions: What You Need to Know
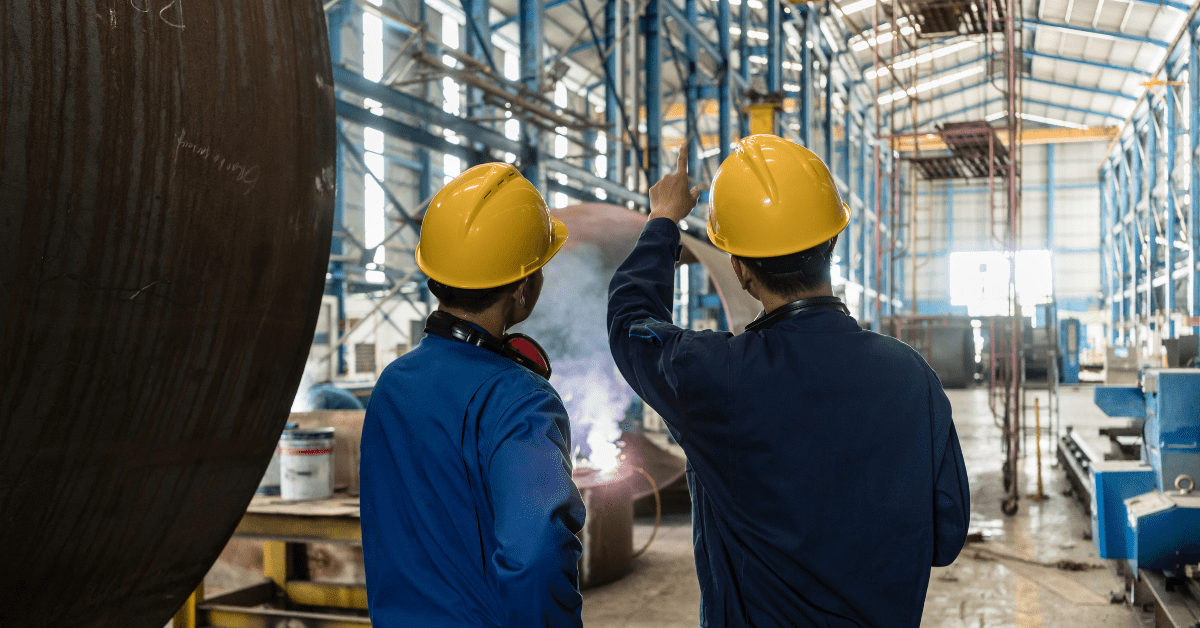
In industries like construction, manufacturing, and energy, efficient and precise fabrication is crucial to building high-quality structures and products. Fabrication solutions encompass a range of services and techniques used to transform raw materials into specific components or assemblies, providing custom-made parts tailored to each project’s unique requirements. From structural steel frameworks to custom metal enclosures, fabrication solutions play a central role in the creation of everything from large-scale infrastructure to complex machinery. Here’s what you need to know about fabrication solutions, the services they offer, and why they are essential across industries.
What Are Fabrication Solutions?
Fabrication solutions refer to the processes and services involved in creating customized parts, components, or structures from raw materials like metal, plastic, or composite materials. These solutions include a variety of fabrication techniques—such as cutting, welding, bending, and assembling—to produce everything from small components to full assemblies for large construction projects.
Fabrication providers use specialized machinery, skilled labor, and advanced technology to ensure accuracy, quality, and consistency in the components they produce. Fabrication solutions can be tailored to meet specific project needs, whether that’s custom structural supports for a building, precise metal parts for equipment, or specialized assemblies for energy infrastructure.
Key Fabrication Services and Techniques
The scope of fabrication solutions is broad, covering several techniques and processes designed to produce high-quality components. Here are some of the core services typically offered:
Cutting and Shearing
– Cutting is often the first step in fabrication, where raw materials are cut down to specific dimensions. Techniques like laser cutting, plasma cutting, and waterjet cutting allow for precise cuts, reducing material waste.
– Shearing, a method of cutting materials without generating heat, is commonly used to produce clean cuts in sheet metal, especially for thinner materials.
- Welding and Joining
– Welding is an essential fabrication technique, used to fuse materials together, creating strong, lasting bonds. Common welding methods include MIG, TIG, and arc welding, each chosen based on the material type and the specific strength requirements.
– Joining techniques also include riveting, bolting, and adhesive bonding for non-metallic materials or where disassembly may be needed in the future.
Forming and Bending
– Forming and bending processes shape materials into the desired configuration without cutting or removing material. These processes use techniques like press brakes, roll forming, and tube bending to create structural components, brackets, and custom shapes.
– Precision in bending and forming is crucial to maintaining structural integrity and ensuring parts fit seamlessly into the final assembly.
Machining
– Machining involves removing material to achieve precise dimensions, using equipment like lathes, milling machines, and CNC (Computer Numerical Control) machines. CNC machining, in particular, enables high accuracy and is ideal for complex shapes and intricate details.
– Machining is commonly used for parts that require tight tolerances, such as mechanical components, fittings, and tools.
Finishing and Coating
– Finishing processes improve both the appearance and durability of fabricated parts. Services can include painting, powder coating, polishing, and galvanizing, which protect metal components from corrosion and wear.
– Custom finishes and coatings add value to fabricated parts, making them more resistant to environmental factors and aesthetically appealing.
Assembly and Testing
– Many fabrication providers offer assembly services, combining fabricated components into complete assemblies. This is especially useful for complex projects where multiple parts must be joined and tested before installation.
– Testing ensures that fabricated components meet industry standards and project requirements, validating factors like strength, durability, and precision.
Why Fabrication Solutions are Essential Across Industries
Fabrication solutions are the backbone of many industries, enabling the creation of components that are tailored to specific applications. Here’s why they’re essential across sectors:
Customization and Precision
Each industry has unique requirements, and fabrication solutions provide the flexibility to produce parts that meet exact specifications. Custom fabrication allows companies to design components that precisely fit their needs, enhancing functionality, safety, and overall performance.
– Examples: Structural steel beams tailored for specific building loads, custom enclosures for machinery, and precise metal parts for automotive applications.
Efficiency and Cost Savings
Working with a dedicated fabrication provider can save time and resources, as these companies have the expertise and equipment to produce high-quality components quickly and cost-effectively. Custom fabrication can also reduce waste by ensuring materials are used efficiently.
– Examples: Pre-fabricated assemblies for construction projects, efficient material usage in aerospace parts, and on-demand components for equipment repair.
Enhanced Quality and Durability
Fabrication solutions use specialized equipment and skilled labor to create parts with high precision, which contributes to greater durability and performance. By employing quality control practices, fabrication providers ensure that each component meets stringent standards, reducing the likelihood of defects.
– Examples: Welded steel structures for industrial buildings, machined parts for medical devices, and corrosion-resistant coatings for marine equipment.
Scalability for Large Projects
For large-scale projects, such as infrastructure development, fabrication solutions enable companies to scale up production, providing a reliable source of custom parts that can be produced in large quantities without sacrificing quality.
– Examples: Mass production of metal framing for construction, pipeline components for energy projects, and equipment housings for manufacturing facilities.
Innovation and Adaptability
As industries evolve, so do fabrication solutions. Providers are adopting advanced technology, such as CNC machining, 3D printing, and laser cutting, allowing for the production of increasingly complex components. This innovation enables companies to keep pace with industry demands and adapt to emerging technologies.
– Examples: Intricate parts for robotics, customized fittings for green energy projects, and complex aerospace components requiring precision machining.
How to Choose the Right Fabrication Solution Provider
Choosing the right fabrication provider is crucial for project success. Here are a few factors to consider:
- Capabilities and Equipment: Ensure that the provider has the necessary machinery, such as CNC machines, laser cutters, and welders, to meet your project needs.
- Experience and Expertise: Look for a provider with experience in your industry, as they’ll have a better understanding of your specific requirements and standards.
- Customization and Flexibility: A good provider should offer custom solutions and be able to adapt to changes in project scope or design.
- Quality Control: Ask about their quality control practices, including testing and inspection, to ensure that components meet required standards.
- Turnaround Time and Scalability: For large or time-sensitive projects, check the provider’s ability to scale production and meet deadlines without compromising quality.
- Reputation and References: Research reviews or request references to ensure the provider has a track record of delivering high-quality fabrication solutions.
Final Thoughts
Fabrication solutions are integral to industries that rely on custom, high-quality components, from large-scale construction projects to precision manufacturing. By using specialized techniques and advanced technology, fabrication providers create parts that meet exact specifications, enhance project efficiency, and improve overall quality. Whether you’re looking for custom metal parts, structural components, or complex assemblies, the right fabrication provider can make a significant impact on your project’s success.
As industries continue to innovate and expand, fabrication solutions will remain essential, offering the flexibility, precision, and scalability needed to meet evolving demands. Choosing the right provider allows companies to unlock the full potential of custom fabrication, ensuring that each component is built to perform, last, and exceed expectations.
Ready to power your next project? Explore our
Fabrication Services, and let’s build something strong together.
Contact us today to learn how Wikota’s Fab Shop can help with your fabrication needs.
Serving North America – We ship completed projects anywhere in the US.